Mark Oglesby

Bruce Butler
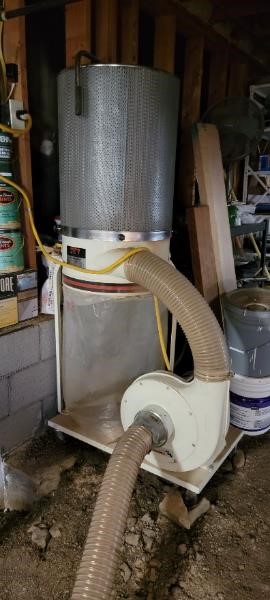
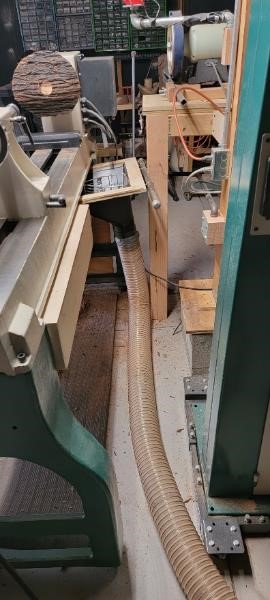
He uses a wireless remote switch that he’s attached to his turning smock so that he can remotely switch the dust collector on and off. The cost is about $23 at Amazon. It accommodates 120 or 240 volts and up to 40 amps. When buying a remote, it’s important to check all the electrical needs of the equipment to make sure it will work. A member had blown out a circuit board on some equipment because he was using a remote that was undersized for his needs. The remote Bruce uses can be found at:
https://www.amazon.com/dp/B0899DSSJM/ref=cm_sw_r_apan_i_QFVJC1021TP154YMBAST?_encoding=UTF8&psc=1
Bruce had originally placed the funnel in a vertical direction but changed to horizontal to catch more chips and successfully prevent them from falling on the floor.
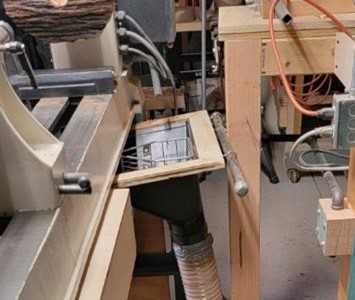
Gary Frank
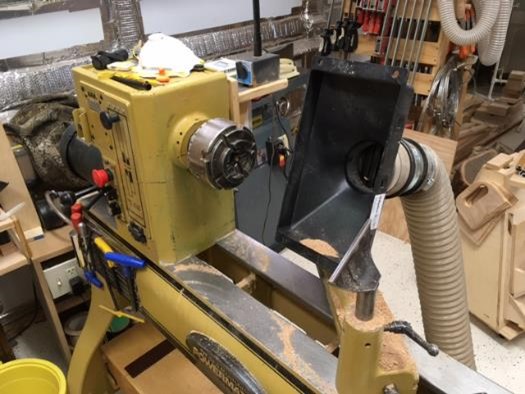
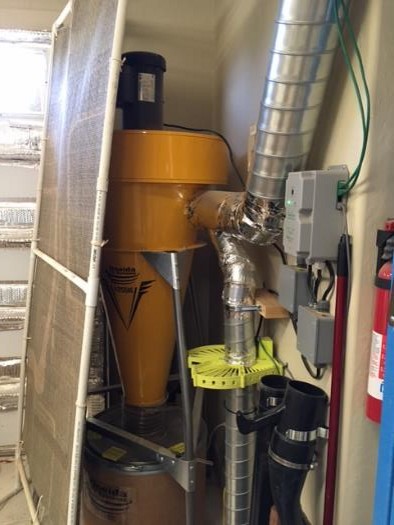
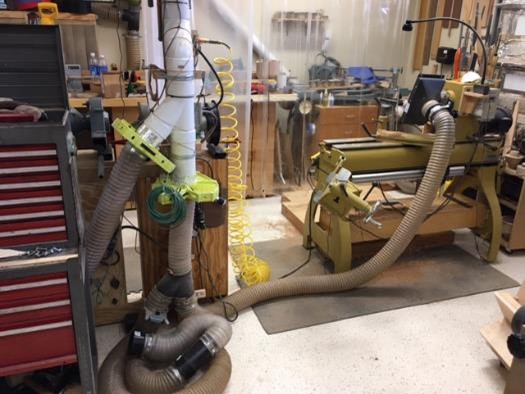
In his whole system, he has 5 or 6 automated gates and a series of mechanical gates. His system has evolved over time. He started with PVC and then changed some to metal tubing. He added bare copper wire to dispense static charges. Someone mentioned that there is wire in the flexible tubing that could be connected to ground so dust doesn’t stick to the outside.
Gary has two air filters hanging from the ceiling and wears his Powercap vent hood or an N95 mask at all times while in his shop to protect his lungs.
Bill McDonald
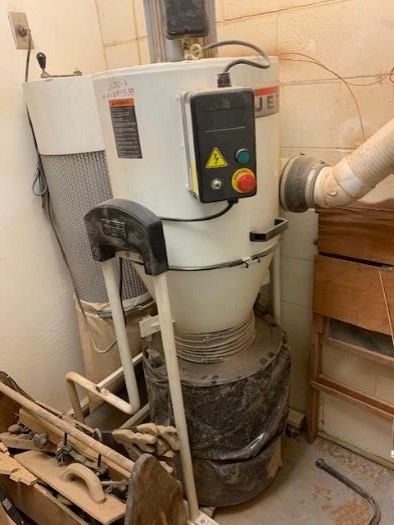
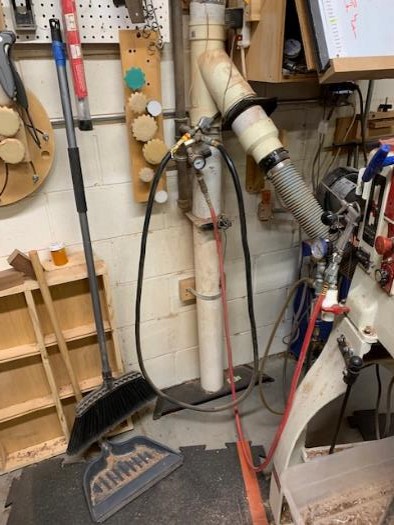
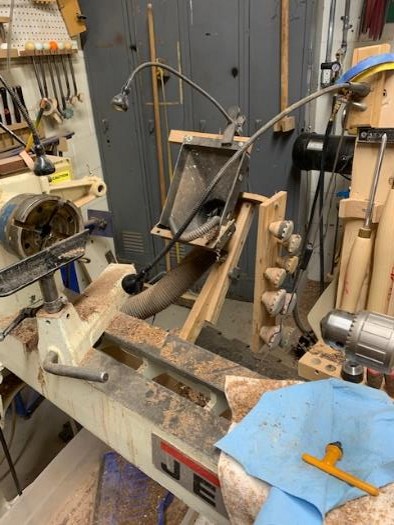
His black hole funnel is located behind the lathe and has bars in it to keep big things out of it. He built a ‘shroud’ on a frame with adjustments that allow him to adjust the angle of the funnel to the area needed.
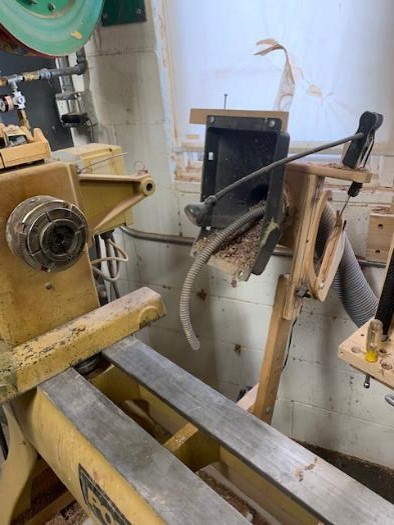
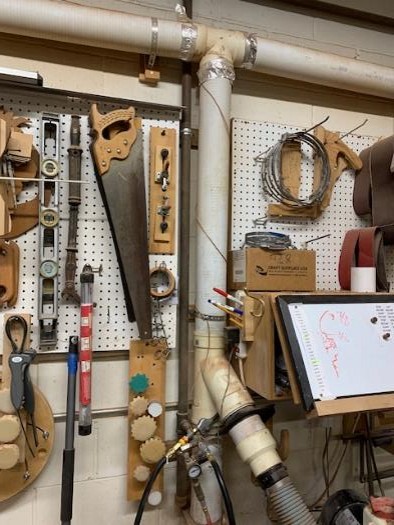
The PVC pipe goes all around his shop for a distance of about 60 feet. It’s grounded to reduce static but does collect dust on top of it. He used aluminum tape to attach the lengths of pipe and keep the system from leaking. It’s not glued together in case he has to clean out an area. He does have a T joint but should have had a Y joint for better air flow.
The hose on the lower part of the photo is the one that goes to the lathe (in an earlier photo).
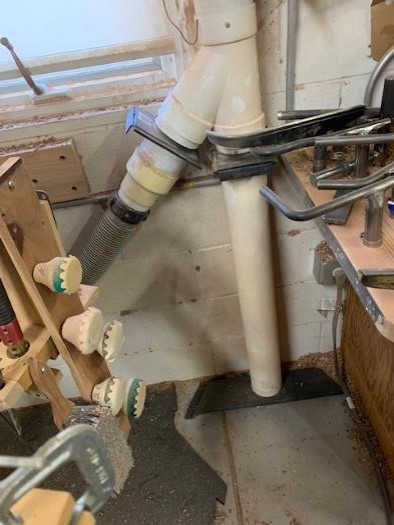
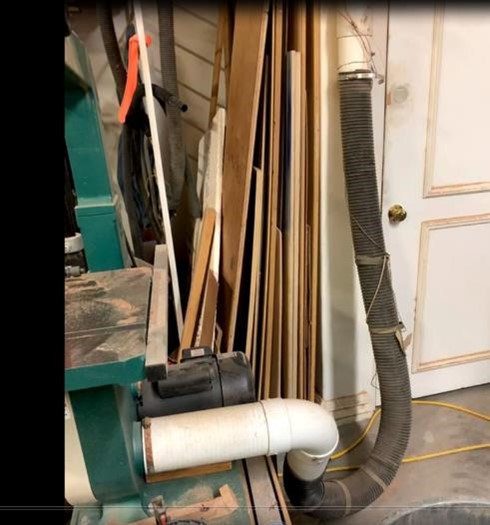
Mike Mitchell
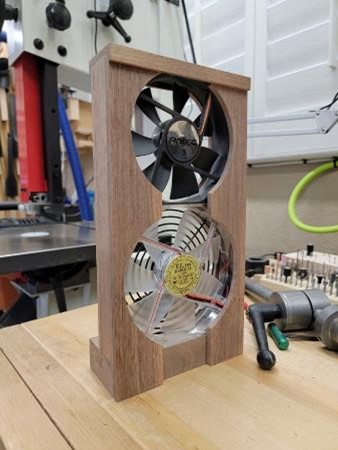
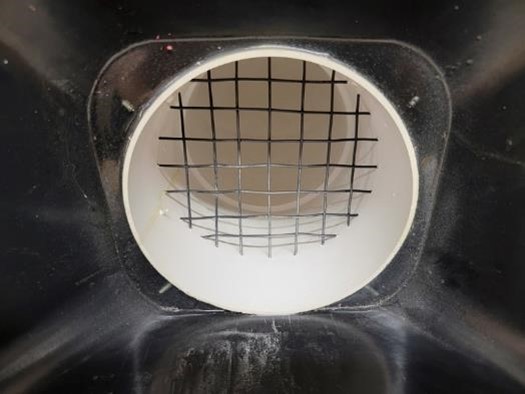
This funnel is located at his carving station and is connected to his dust collection system. He used 6” PVC pipe and epoxy to fuse the PVC to the black housing since the correct size wasn’t available. He drilled small holes in the PVC and used electrical bell wire that he wove across the area to prevent big things like paper towels or sandpaper from entering the system.
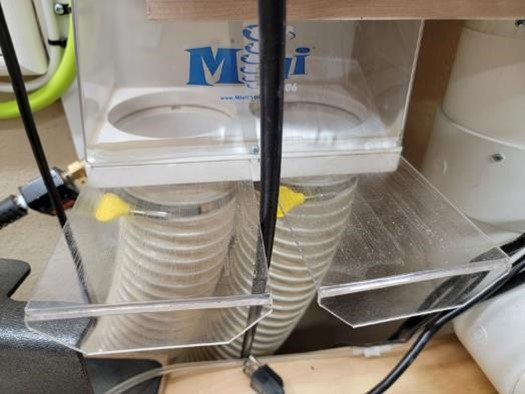

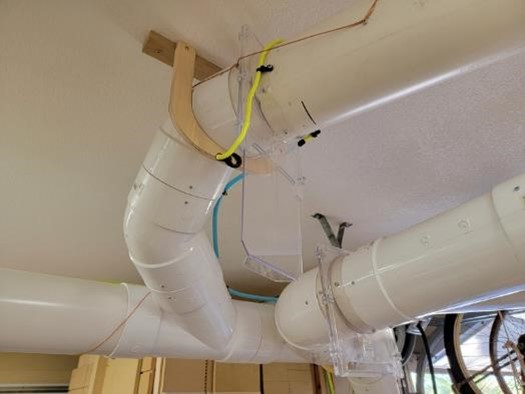
Six-inch sewer pipe was used for the system along the ceiling with Y angles that provide a good flow through it. Two 45° angles were used instead of using a 90° at any point. Stranded copper wire from Rockler is wrapped around screws for grounding. Non-insulated small gauge copper wire could also be used. The yellow tie at the top is used to prop up the gate that doesn’t always stay closed because of its vertical position. Information about dust collectors can be found at:
https://www.clearvuecyclones.com/why-clear-vue-cyclones/
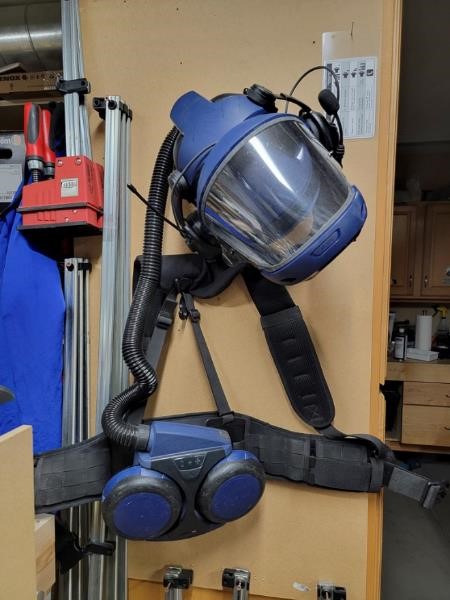
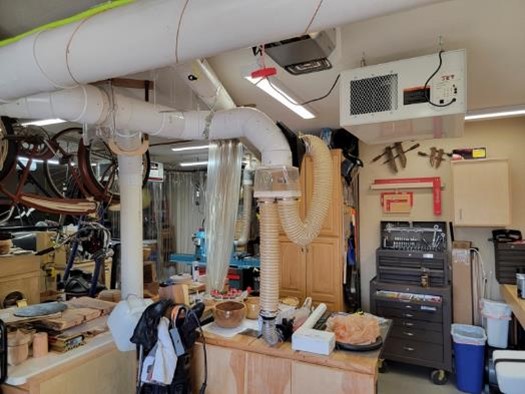
His system is routed to the lathe (in the back), his table saw (front center) and the router table (on the left). He moves the flexible hoses to the area needed when using the dust collector. He has two Jet air filters on the ceiling. He also has mounted copper pipe in a 10’ square around the lathe with 5’X8’ clear shower curtains to contain the chips when turning. The chips drop down along the plastic. (It was also mentioned that an old ironing board makes a good outfeed table for a table saw.)
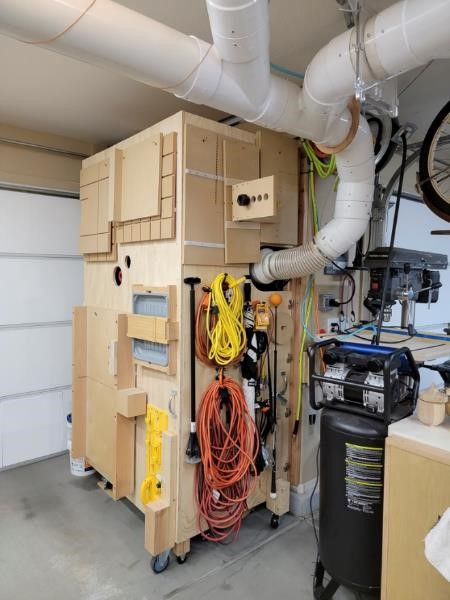
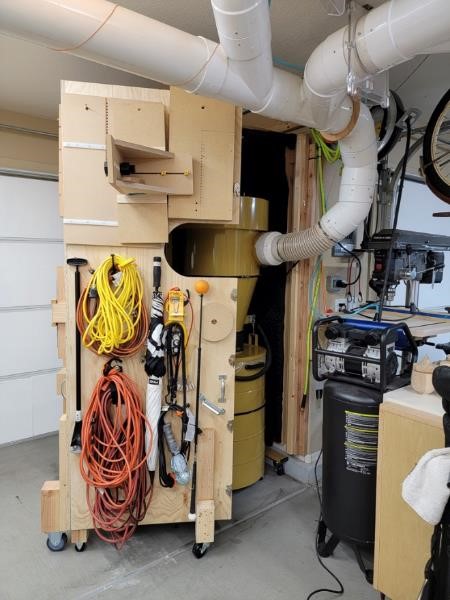
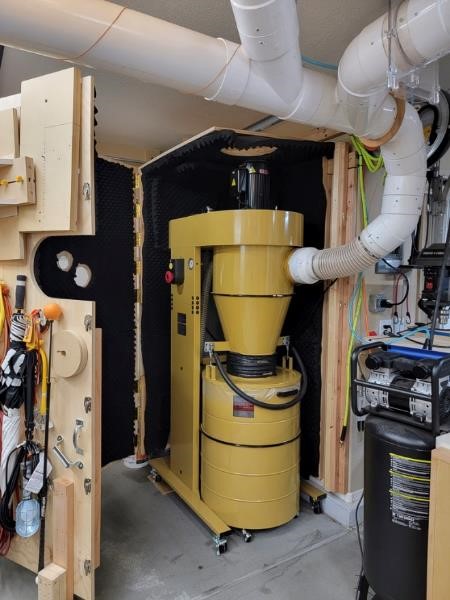
The black sound insulation was applied on all side and the top. He uses a remote to turn the system on and off.
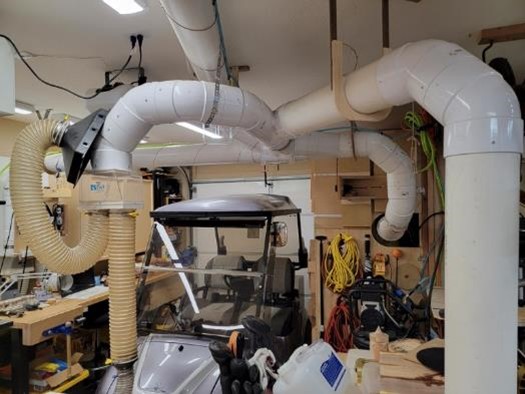

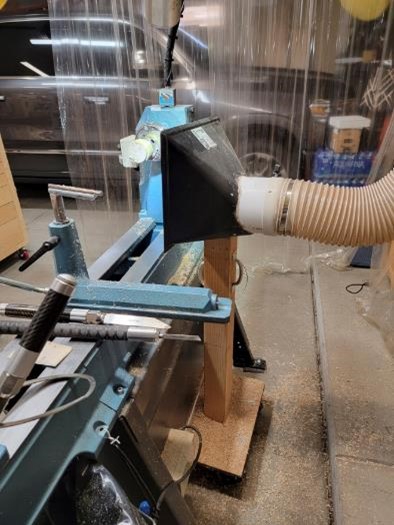
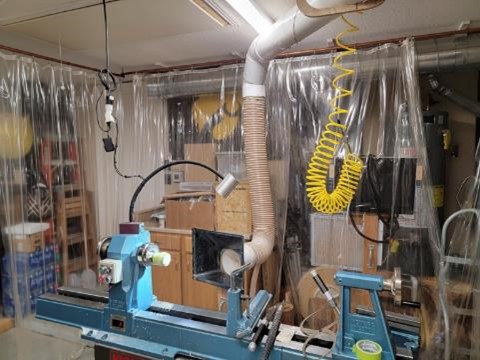

An article about a piece shown during ‘show and tell’ was on the AAW website. It was called ‘Turning Six Diamonds’ by Peter Exton. https://higherlogicdownload.s3-external-1.amazonaws.com/WOODTURNER/AW2706p36-44.pdf?AWSAccessKeyId=AKIAVRDO7IEREB57R7MT&Expires=1649878307&Signature=xRVs%2Fch2FbxxqgBVPqi5z6IGSGY%3D
More pictures and comments about dust collection were submitted than there was time to include in this session. A ‘Dust Collection, Part 2’ discussion will be part of Chips and Grits in the coming months.