Jerry Shugars
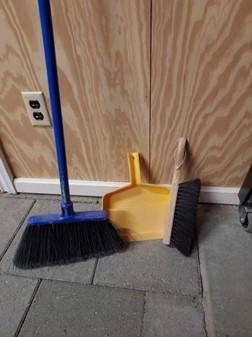
How do you get rid of sawdust? The trash seems the most common place. Some people have used chips in horses’ stalls, but some woods are toxic. Some recycle into gardens, but not walnut since it’s dangerous for plants. A
vendor at the Farmer’s Market collects plain chips (no pine) and makes compost that he sells at the market.
A dustpan with a long handle makes the job of picking up chips easier. (Such as the ‘quickie jobsite jumbo dustpan with handle’ at Amazon)
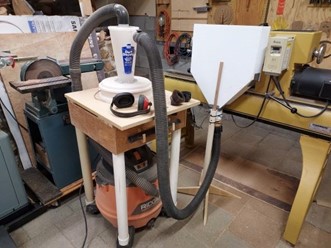
He uses headphones for ear protection from the noise.
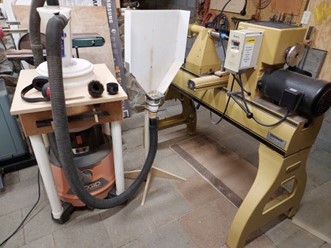
The hardest part was attaching the pieces together, but lots of duct tape helped with that.
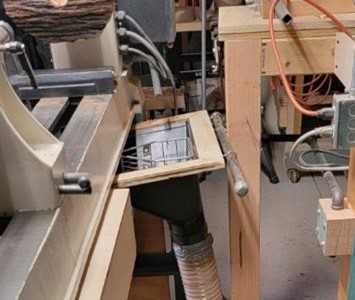
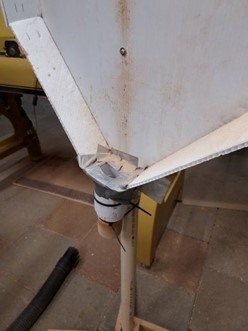
Using an air filtration system, broom and dust pan, and cleaning on a frequent basis are better for health and breathing.
An inexpensive way to build a filtration system that is often used in schools is the Corsi-Rosenthal box. This is a cube made from furnace 20X20 filters around a fan. Instructions and information can be found at https://cleanaircrew.org/box-fan-filters/. A member recently made one for around $100 to filter and reduce the pollen in his house.
Jerry Walters
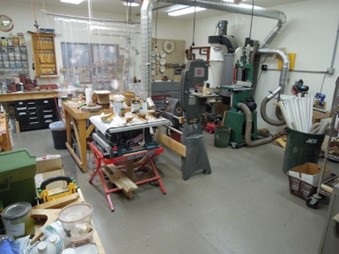
A shower curtain is hung from the ceiling behind his lathe. It contains the dust and keeps heavy debris from being thrown beyond the area.
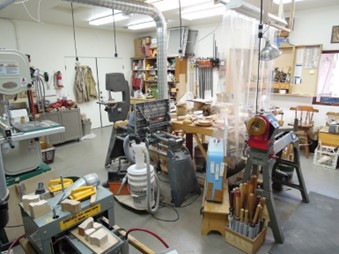
The fire extinguisher for safety reasons and the wall phone were noticed by all. The landline phone will work for emergencies if power is out or cell
phone service is unavailable.
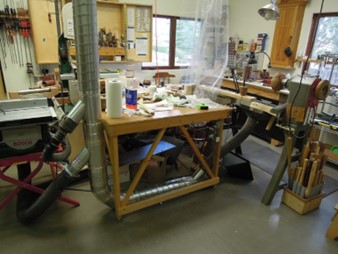
A funnel on the floor under the lathe is used as a floor sweep. He runs his system all of the time so it’s trying to pull the dust downward and not into the air.
It’s easier to leave the larger shavings on the floor and scoop them up than to empty them out of the system. There’s not a blast gate on this part but
he can put a piece of plywood over it if needed.
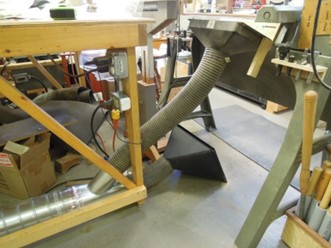
He cautioned that care should be taken when using the cyclone system because metal, such as bolts or screws, can cause sparks. Also, the dust collection system should not be used when woodburning. The area should be cleaned well first.
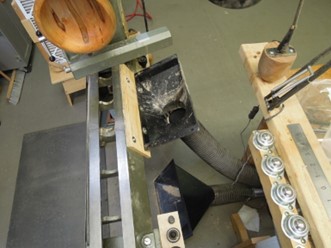
Aluminum duct doesn’t spark but galvanized steel can spark.
One member was shocked while using his planer. He attached some 14-gauge wire to some bare metal to ground it.
Static charges can also cause problems with buffing systems. One member fried his lathe control system due to a static charge. A rubber fatigue mat on the floor can help. One member wears a conductive wrist strap when buffing to bleed off the electrostatic charge. He attaches it with blue tape to the lathe bed and tapes it to his lower leg. He has less mobility but it’s worth it to avoid an unexpected shock. Those static shocks can affect implants such as hearing aids and pacemakers. Another member runs a wire to a copper bracelet to prevent a shock.
Pete Lang
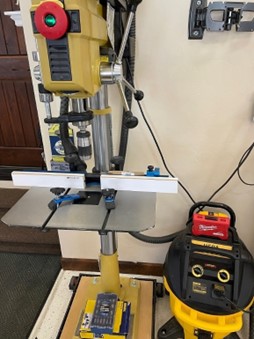
When his dad was young, there were no dust collectors and, due to smoking and dust from his shop, his dad had to use oxygen the last years of his life. To avoid that, Pete usually wears a mask and uses his dust collection devices.
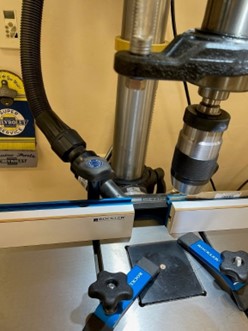
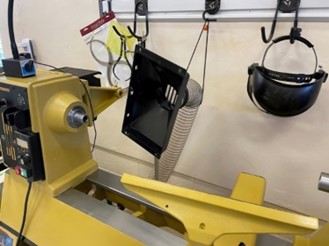
This view shows the hood and attachment of the dust collection system to the lathe. It’s attached through a 4” flex hose line.
He mainly uses this while sanding projects.
Pete prefers the Elipse P100 dust mask because it doesn’t fog his glasses. The filters can be cleaned and last about a year. The entry on Amazon has a video and lots of information about these masks. (https://www.amazon.com/GVS-SPR457- Elipse-Respirator- Medium/dp/B013SIIBFQ/ref=sr_1_1?keyw ords=Elipse%2BP100%2BDust%2BMask&qi d=1652287374&sr=8-1&th=1)
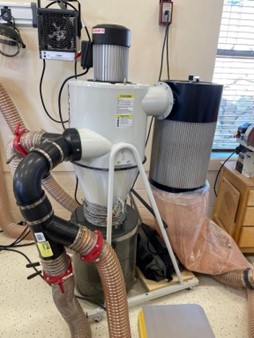
The canister collects the heavier chips while the finer dust collects in the bag. The red coloring in the bag is padauk sawdust that is as fine as cayenne pepper. That fine dust is the most dangerous to our lungs. The blast gates on the flex line (lower left) are butterfly valves that are described later in these notes. (closeup photos below)
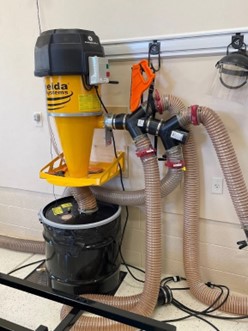
A wire along the top goes from a sensor to a light that indicates when the drum needs to be emptied.
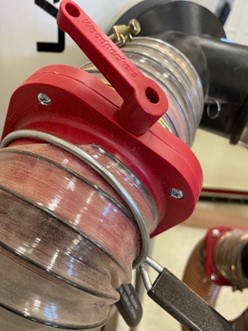

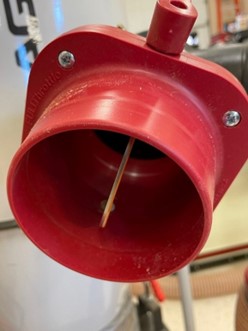
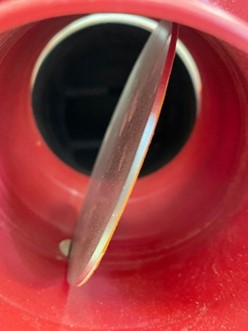
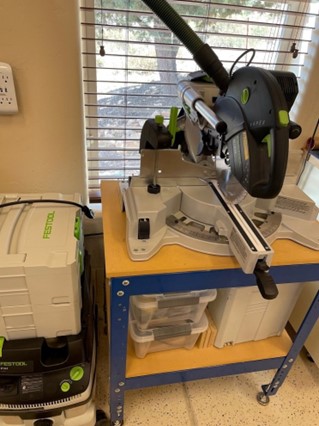
Dean Humphrey

plastic bag doesn’t get suctioned into the system.
The red handle is a broom that he moves through the element each week to release the dust from the filter. There is a lot of heat from the system, so he has a vent up high above it.
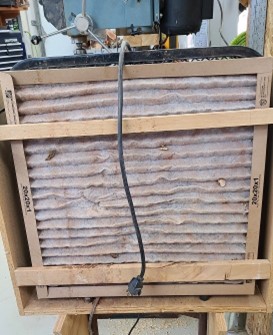
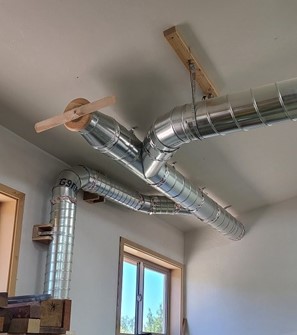
The duct work from his dust collector has branches that are at a 45° angle and narrow from an 8” to 6” pipe as it goes to his sanders and planer.
The (B-52) propellor is on a section that’s capped off with caulk to prevent air leakage.
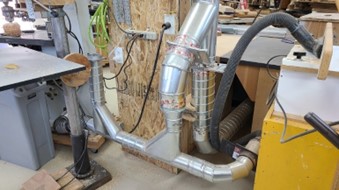
His ducting was made by Empire Metals and is sealed inside with caulking.
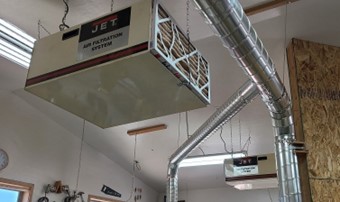
One problem with the remote is that fluorescent lights interfere with the remote transmission. Dean has added a Kasa switch, turned on with his phone, to bypass the problem. Other members have had similar interference problems with the Jet system.
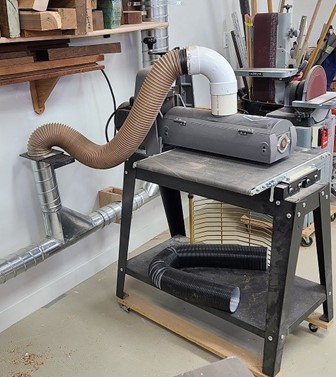
Another member shared a warning about belt sanders. There’s no dead man’s switch for the feed belt, only the rheostat switch. His hand had been pulled into the gap and took a chunk off his finger. He suggested everyone add a switch that could prevent this problem.
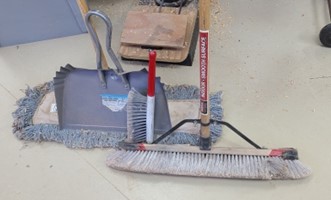
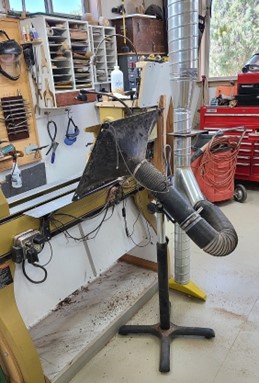
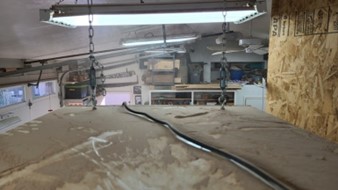
Wind blowing through the shop can be the best air cleaner since dust settles in a closed system. Dust settles on lights,
switches, etc.
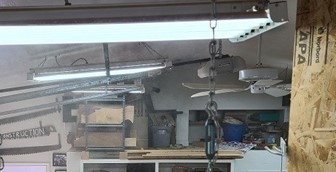
A few resources were suggested for more dust collection information. Jay Loden showed a video of an R2D2 style of dust collector that can be moved around in the shop which might be helpful for those with limited space. It can be seen at https://www.axiomstratus.com/.
Also, Woodcraft has a blog that can provide more information to woodturners. Find it at https://www.woodcraft.com/blog_entries/dust-collection-solutions-for-the-home-woodshop