Jerry Walters
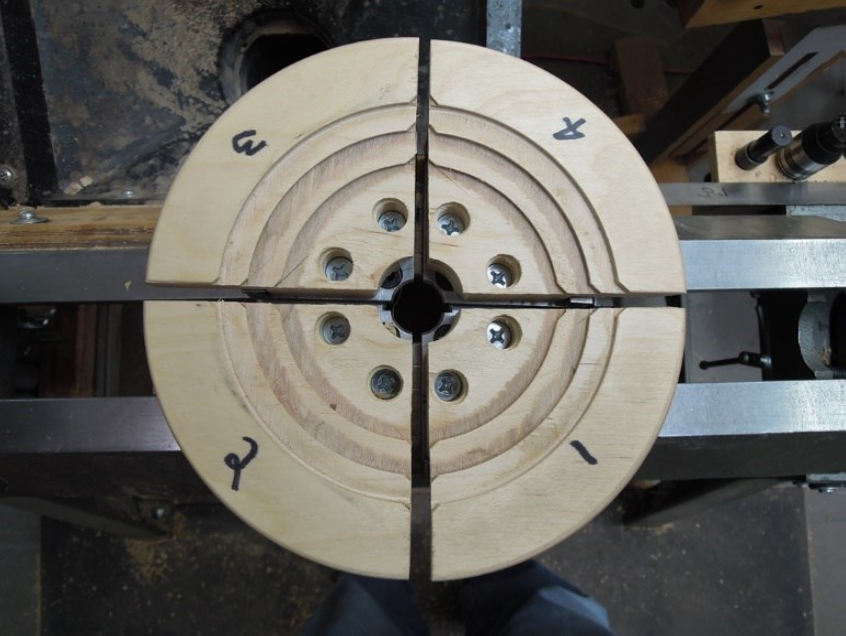
These are Baltic birch step-jaws that were made for a 130 mm Nova scroll chuck. He used ¾” and ½” birch fused with TiteBond original to make the jaws. Before cutting out the steps, he put ¼” plywood between the jaws to make a more perfect circle. He also took off corners to minimize divots in projects. They are numbered to match the chuck.
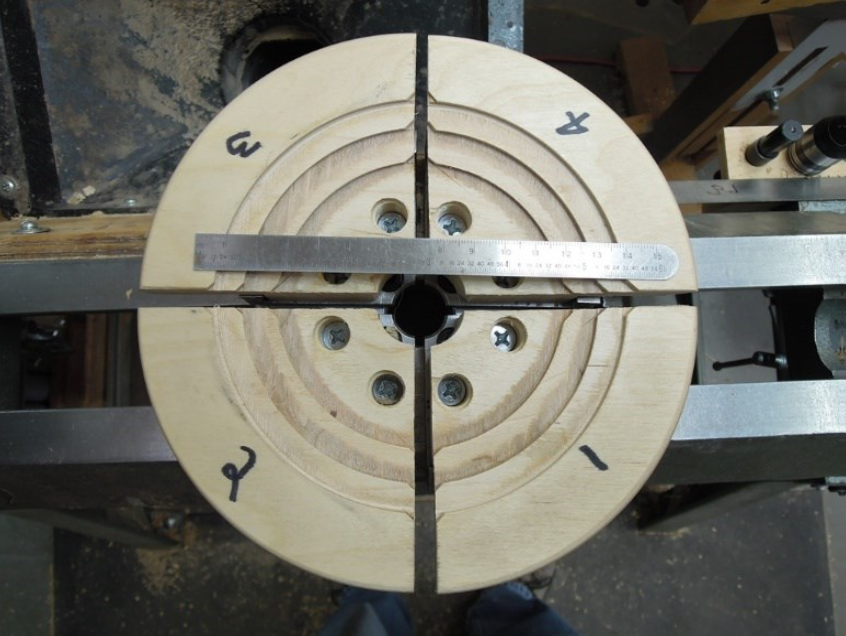
They were built for finishing the bottoms of small bowls or platters that were too small for his Longworth chuck. The jaw size ranges are: 3.5”-3 7/8”, 4.25”-4 5/8” and 5”-5 3/8”.
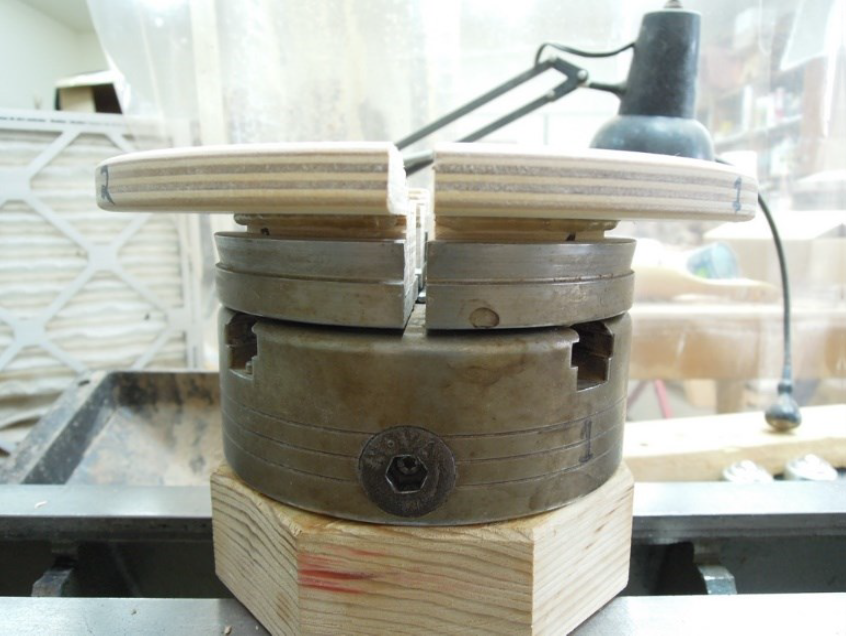
A side view of the step-jaws.
Solid wood with no voids, such as Baltic birch, should be used when making jaws for strength.
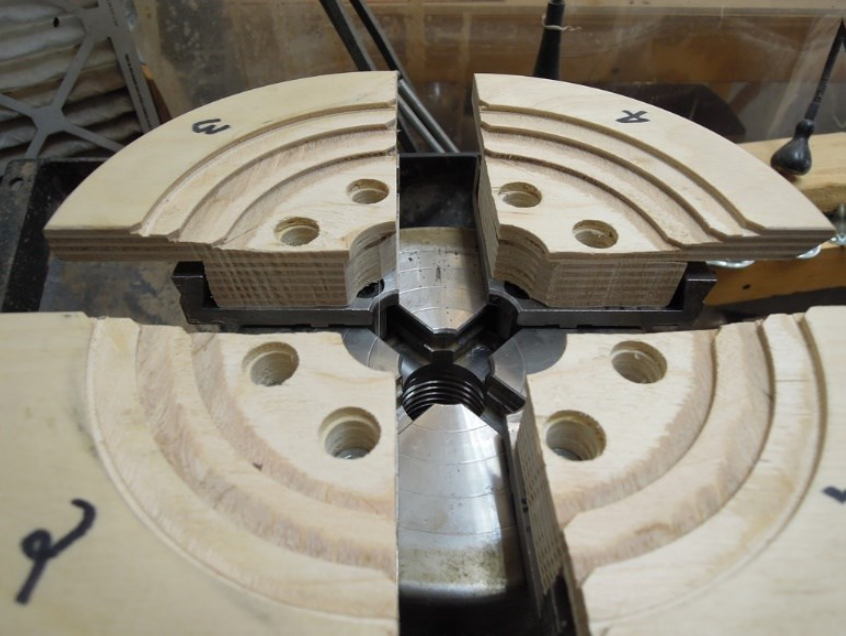
A close up view of the jaws when opened on the chuck. The steps are the thickness of two layers of the ply, which is about 1/8”. There is a very slight dovetail on each step that’s barely noticeable. Although it looks like there’s a small crack in #4 on the right, it’s actually an area where the top veneer area thins toward an edge. There’s glue in the area and since pressure is applied outward rather than upward, there’s no problem with it.
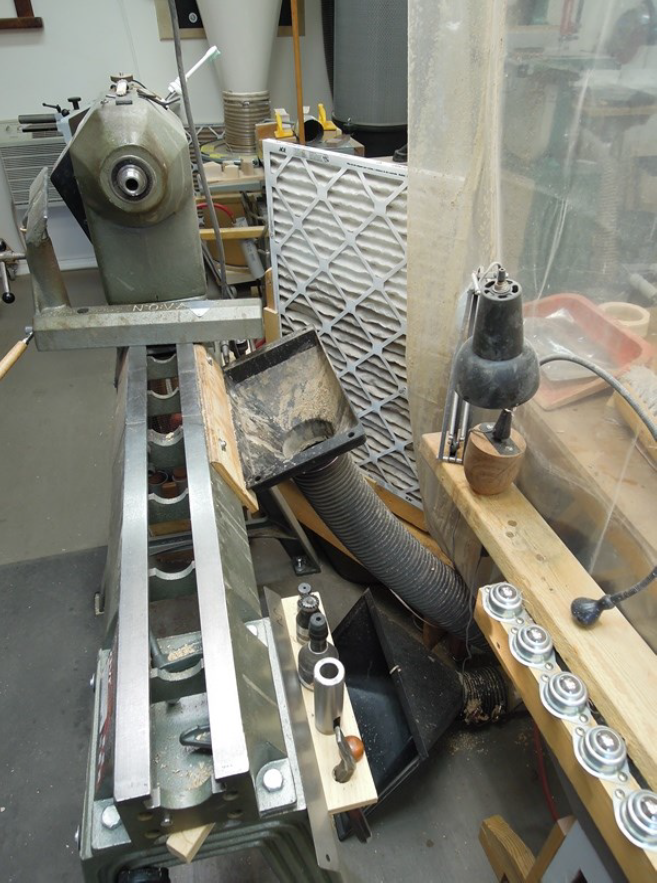
Jerry added wooden shelves to both the headstock (drive centers and wood worm screws) and tailstock (live centers, morse taper extender, knockout bar) to his lathe. He has a sliding bracket to hold the hood of the dust collector that sits below the banjo. He drilled and tapped the apron of the lathe bed and has slots in the plywood to allow it to slide. He puts ½” hardware cloth in the tube to prevent sandpaper from being sucked into the dust collector. There are two lines for the dust collector system. The top one is very effective in removing dust when sanding. The lower one was primarily for chip collection, but it’s less of a hassle to sweep them up than empty the bin. When sanding, Jerry uses a paintbrush and air compressor to remove dust when changing to finer grits. He uses the toothbrush to scrub out the pores in the wood before using sanding sealer and before final finishes.
A few comments about clean up, sawdust and wood chips: Some turners have intelligent chips that are good at avoiding the dust collector. Some chips have even been trained to grab onto socks and crawl into shoes.
Dan Hall
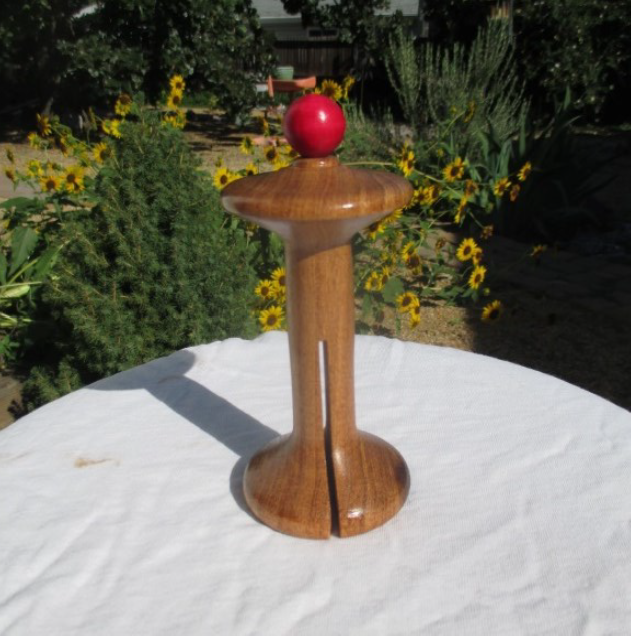
Binding buddy: This is a large spool used by quilters to wrap binding on the spindle. The diameter is 2” across with a 2 ½” spindle. There is a ½” hole drilled inside the slot. Quilters put it on a peg on the wall to hold the binding. It has a tenon on top with a ball that is either turned as part of the piece or added, such as this one was. Due to the slot, it’s important to watch the grain or it could split or splinter when cut.
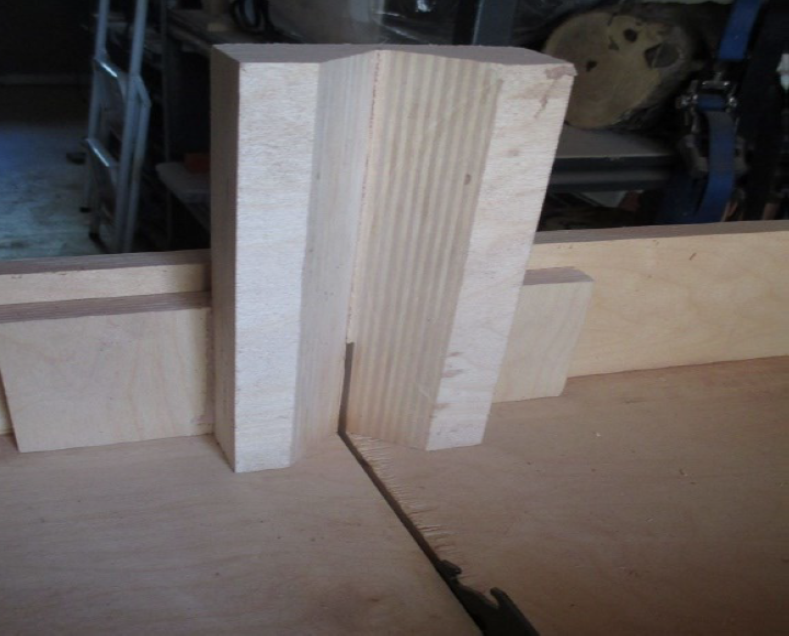
Slot cutting jig: This was made with left over Baltic birch. The two pieces were cut at a 45° angle to hold the binding buddy blank for cutting on the saw. It can be slid along the sled to cut the slot in the binding buddy.
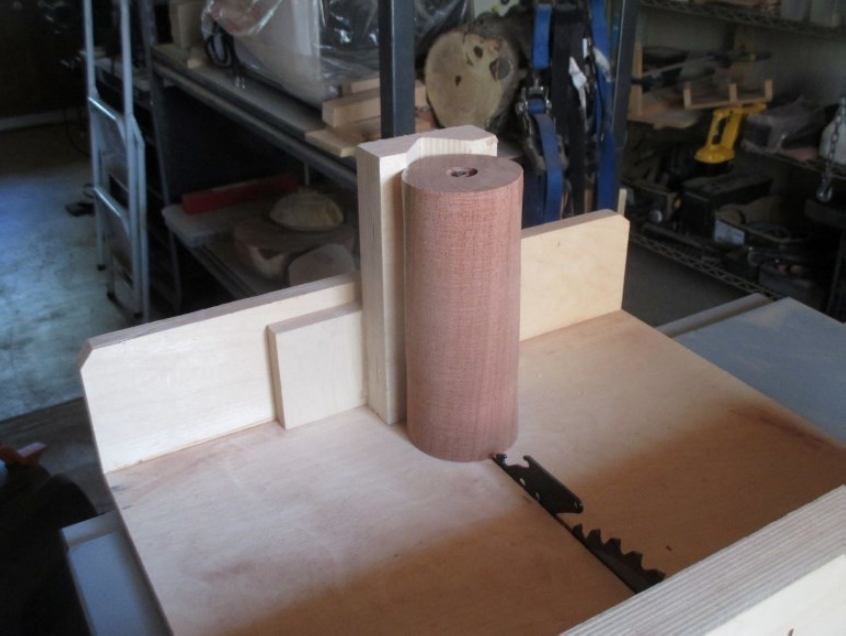
Binding buddy blank: A clamp holds the sled securely in place. The blank fits into the angles of the jig to hold it safely and keep it lined up for the cut. If it’s tall enough, it can be held by hand or may need to be clamped in place. Others mentioned, that if the v-block is turned on its back, it could be used on a bandsaw.
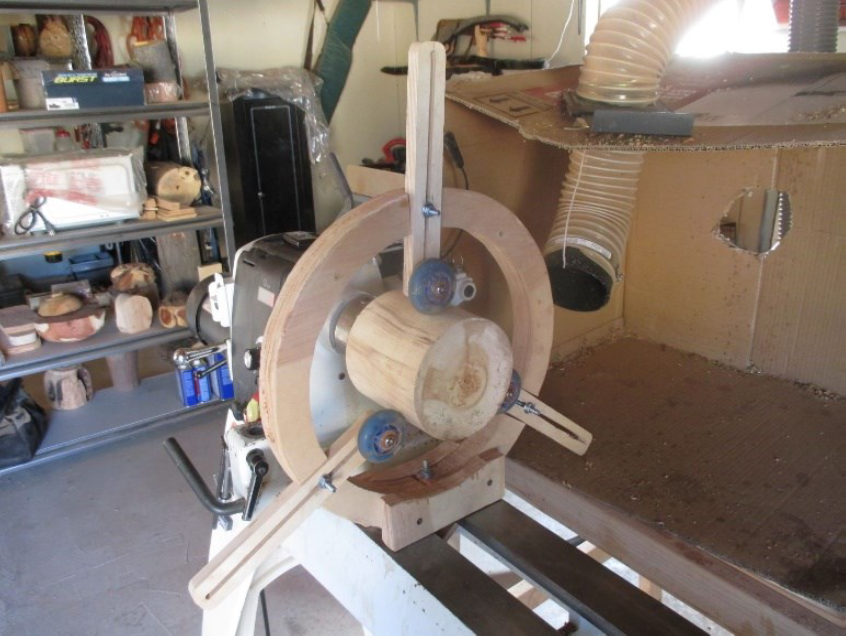
Steady rest: This was made from Baltic birch. The wheels are clear so they don’t leave marks on a project. This is a safer way to hold objects like the one shown. There are routed slots in the arms, which could be shorter (unless a larger lathe is in the future). Dan slips his steady rest along the bed of the lathe end to remove it. Dave Madden suggested a way to attach it with a round cylinder and square block under the lathe bed that can be loosened and removed by lifting it from the bed without removing the tailstock.
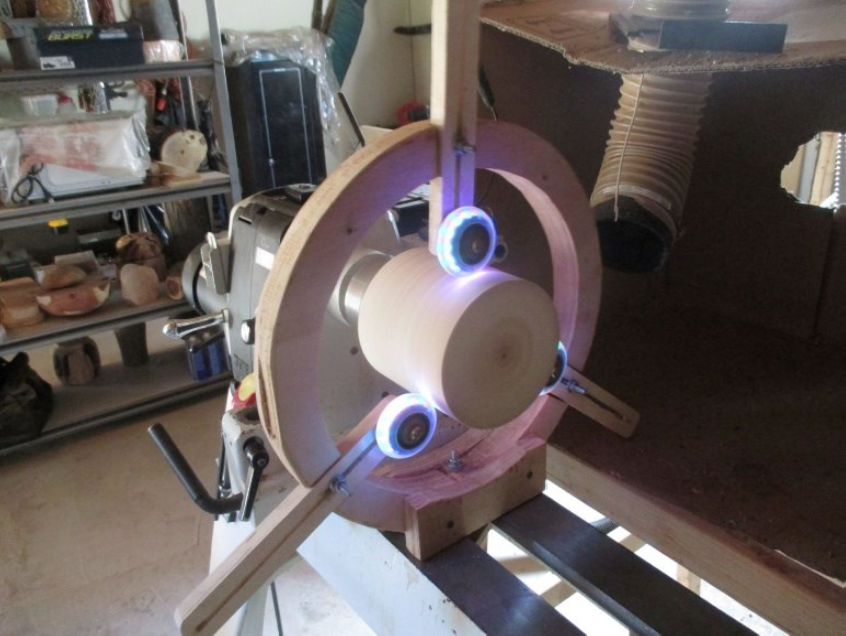
Light show: After making the steady rest, Dan discovered that these wheels light up as they turn. Another member suggested that thrift shops have old inline skates for buying wheels cheaply.
Other discussion on these pictures: There is a wire connected to the dust collection tube that is used to adjust the angle of the tube.
Dan had used an idea from Dave Madden of putting a cardboard box behind the lathe to catch chips. The dust goes up into the dust collector and chips fall to the cardboard. Dave said he also has a hole in the base of the box with a box below it that slides out to dump the chips. That base is elevated 3-4” for the box to fit under it.
Jim Winge
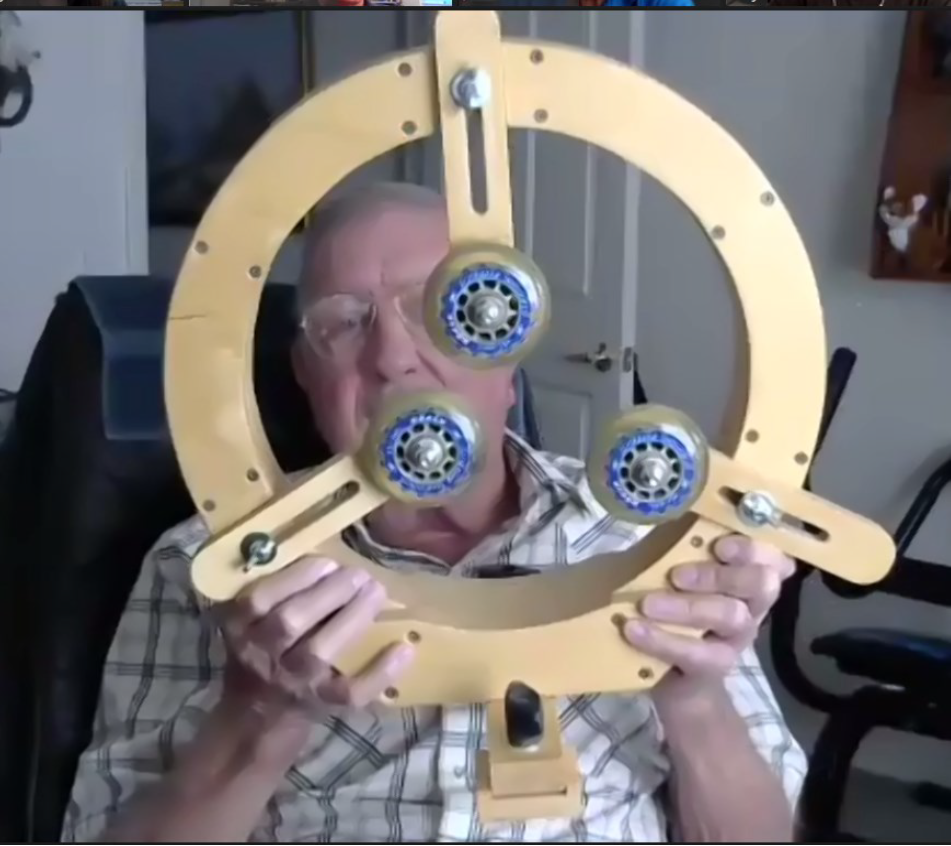
This steady rest was made based on plans from an AAW article. It’s very sturdy and was made from Baltic birch. The arms can be adjusted and moved to locations as needed to support the piece being turned. He not only uses a steady rest on bowls, but also uses one when he’s making tools to hold them while drilling holes.
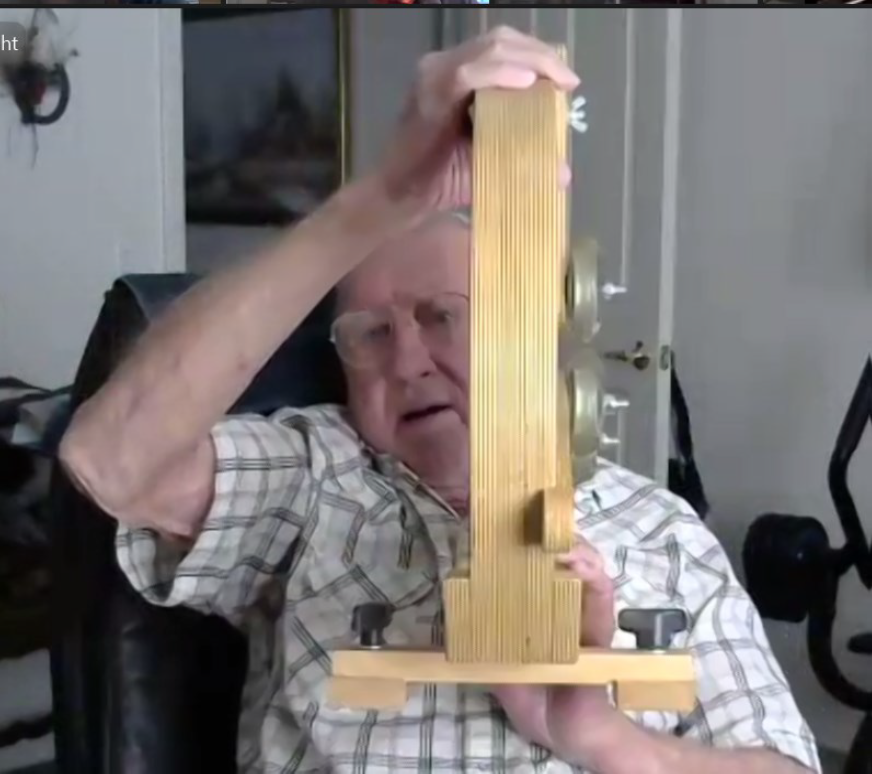
Side view.
Bruce Butler
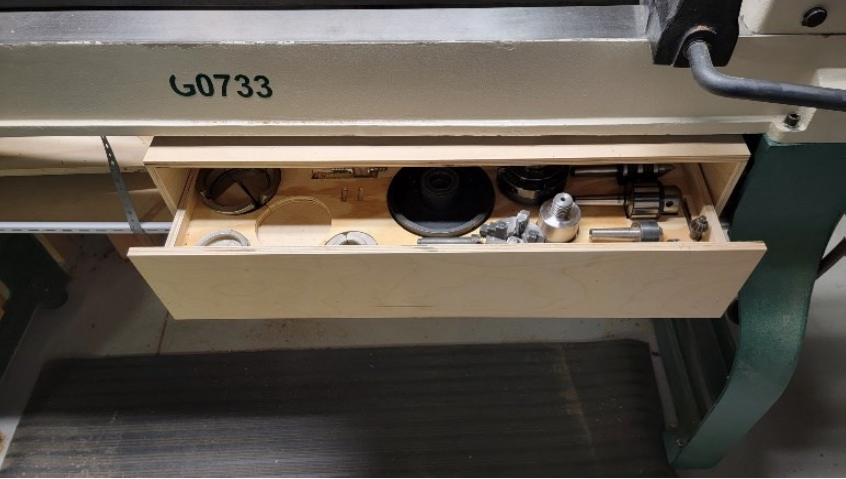
Bruce built a shelf from Baltic birch under his lathe along the long bed of his Grizzly. When the drawer closes, it’s inside the frame and closes completely to keep sawdust out. He used the metal rails that are often used for adjustable closet shelves to support the drawer between the cast legs of the lathe with one pipe strap in the center. The shelf is screwed in from the bottom and is ¼” below the lathe bed. He used ball bearing glides and has a lip on the bottom to pull out the drawer.

Bruce made this vacuum chuck with Trex as a sturdy material that works well to make chucks for the lathe. His pipe is 10-11” long with a foam cover at the end. The bearing is in the light-colored part. The whole thing revolves except the tubing. This works well for small pieces and holds a 21-23 inches mercury vacuum. He has a larger flat chuck with a hole in the center (5” diameter) for larger pieces that holds a similar vacuum.
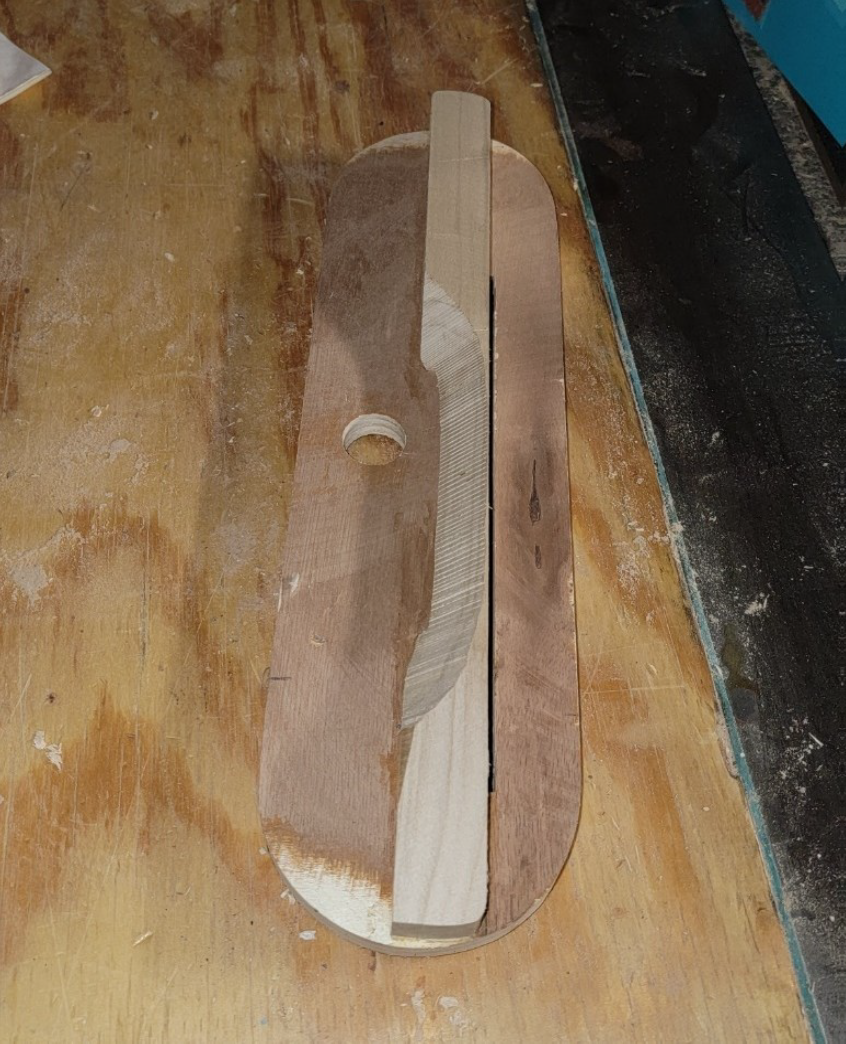
This is an insert for a table saw used in cutting segmented pieces. An angle was cut out on a band saw with a tipped table to give a slope for segments to fall down the slope and away from the saw blade.
Jay Loden

Jay made this finger protector from a piece of leather and elastic to use on his finger when spreading CA glue. He sewed them together on the sewing machine and has used it for several years.

When the CA builds up on the bottom, he sands it down to keep the surface flat. It has helped preserve his fingerprints from being worn away over the years.
Mark Oglesby
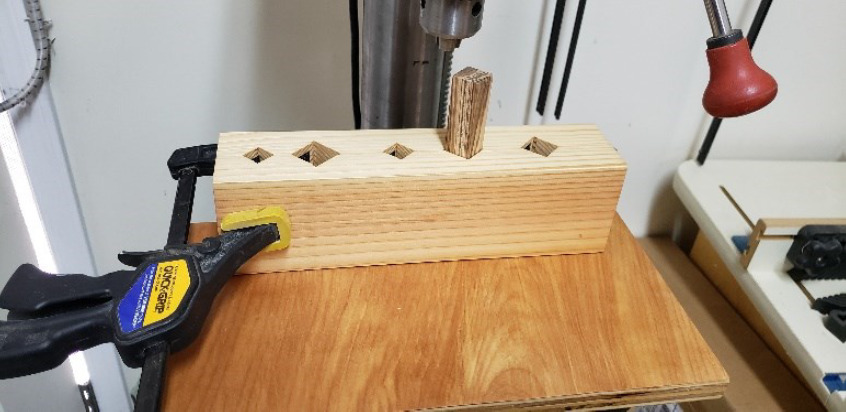
This jig was based on a YouTube design (DIY pen blank & dowel jig vise). It was made from Baltic birch and has various sized holes which were cut out with a table saw. It’s helpful as a portable jig and can be moved to drill according to the size dowel or blank being used.
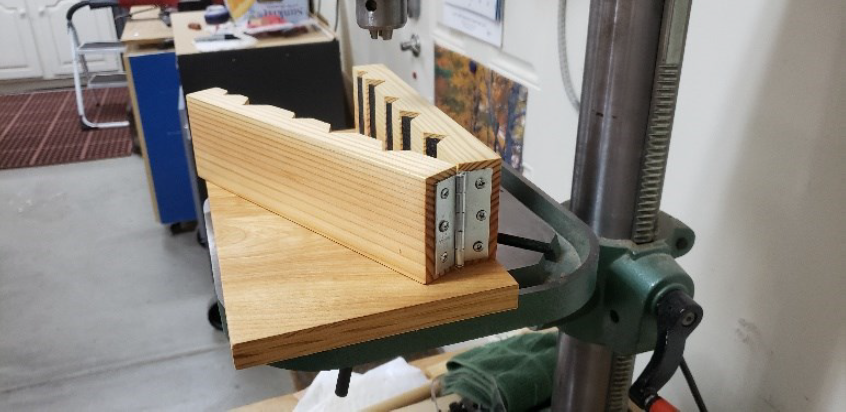
The end is hinged and is screwed in from the base so it’s stationary. It’s very stable when clamped down to the drill press bed.
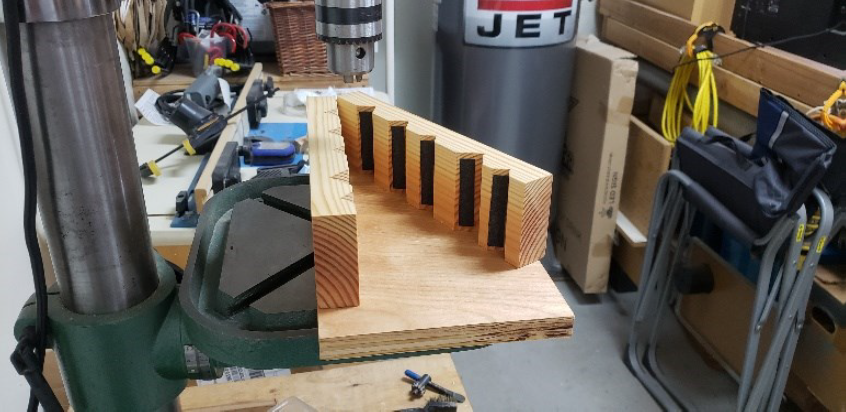
Sandpaper was glued inside for grip, but when Mark tried a pen blank in one, the sandpaper, which had been glued with TiteBond, came loose. Since it’s tight when clamped closed, the sandpaper is probably not necessary. He put a dowel in part way and it still held well when clamped.
The advantage of this jig is that multiple pieces can be drilled with one setup. It gives consistency and allows repeating that step with several projects at once.
The question was asked about blow out on the bottom. With a brad point bit, he has had clean cuts. Often pen turners will put tape on the bottom to prevent that problem.
Another question concerned the drill bit going through the blank or dowel and puncturing the jig. The suggestion was made to dado out the length of the plywood (perhaps ½” deep and 1 ½” wide) along the slots. Then a sacrificial block (perhaps ¼” thick) could be placed along the jig when drilling.
Mike Alder
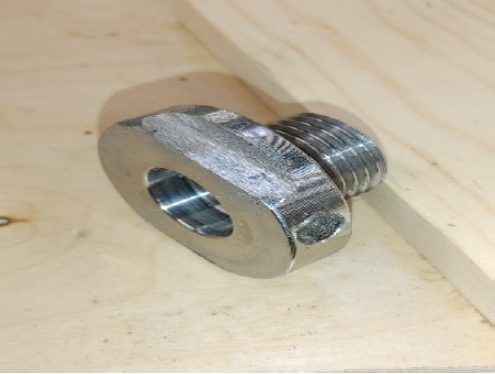
“Need is the mother of invention.”
Mike was making a vase with a zipper in a slot and needed a stable way to hold the piece to cut the groove. He took an old adaptor from a small lathe and cut a 1”- 1 ½” groove on one side.
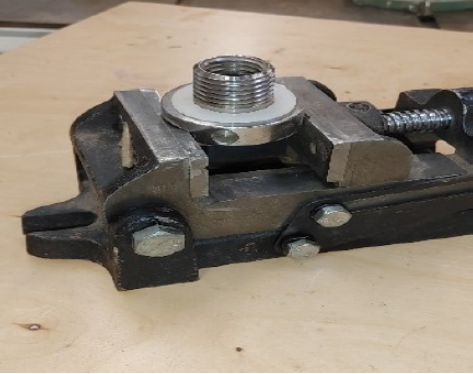
When put into a universal vise, this adaptor allows a piece to be rotated 360° to have access to the different angles when cutting. The vise is clamped to the table for stability.
Others asked if it would help to cut the other side, but he found this to quite stable.
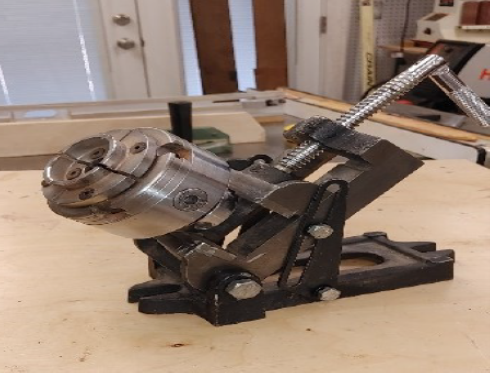
This adaptor is attached to the scroll chuck so the turned piece can stay in the chuck while working on it. A turner can then use it off the lathe and return it with no change in the way the piece is held for turning.
There are universal fittings available for $150, but this inexpensive adaptor he made works well at any angle.
Carvers use similar arrangements to hold items for carving. It’s much safer than holding them between the knees!
Ken Allen
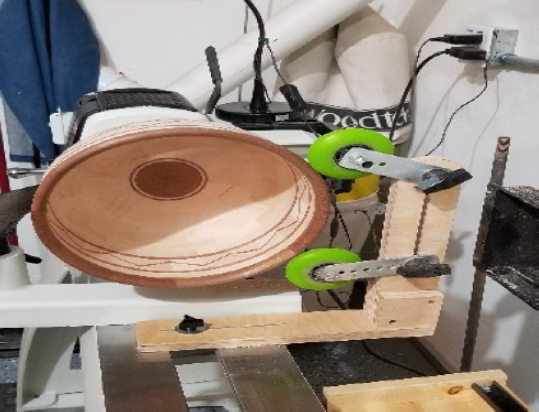
This is a homemade steady rest for bowls made from Baltic birch. Aluminum flat bar was used for the arms, it is adjustable and the knobs can be tightened in the correct location. He would improve his design by putting the pivot points for the two supporting wheels together in the center to form a V angle so the radius would be the same. As it is, the pressure on top and bottom aren’t always the same causing some deformation while turning. It could be reversed so the wheels are on the forward side of the bowl for support on the cutting side. He does place his hand on the outside to dampen the vibration when turning.
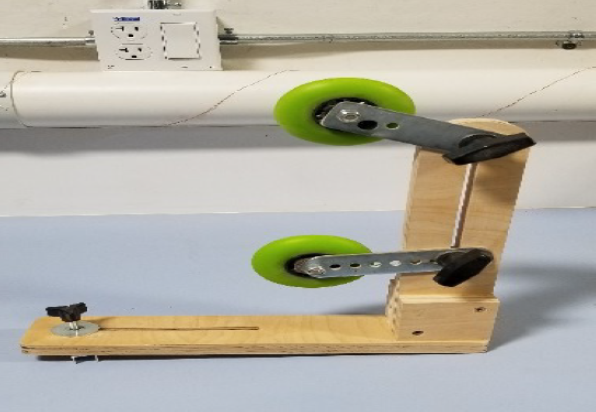
The skateboard wheels are made from a polyester material. They are a soft plastic and there has been no color transfer. You can select the level of hardness when ordering wheels and should avoid rubber.
A steady rest should be used before applying finish. It should be removed before doing the final sanding since the wheels will leave a shiny mark.
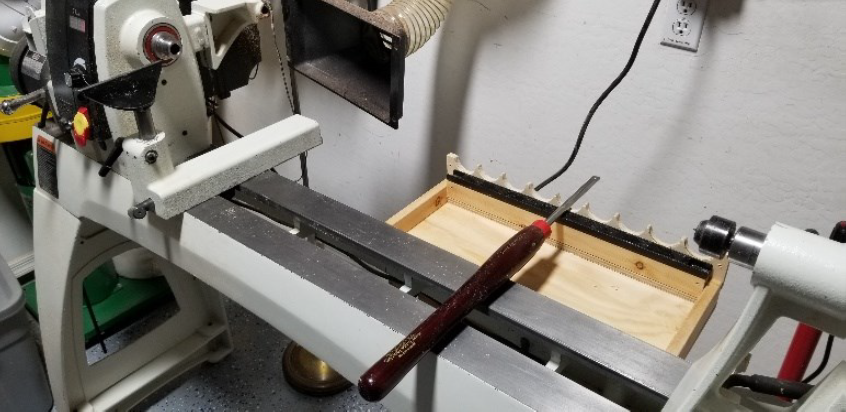
Ken built a shelf that’s attached to the bed of the lathe to hold tools. It has scallops to keep the tools from rolling and has a magnetic bar to keep them in place. It’s helpful to keep small tools handy in the shelf when turning.
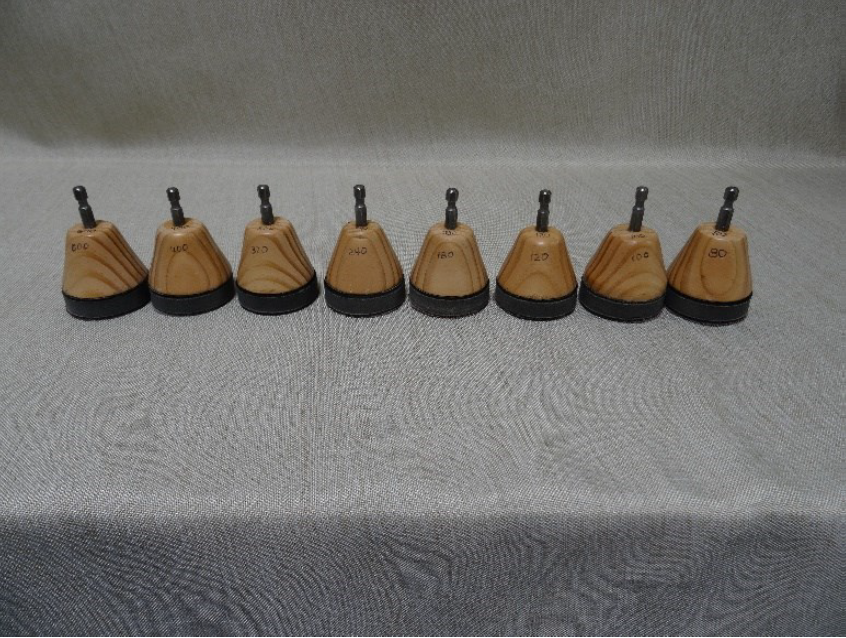
Gary Frank had taught club members to make sanding disks so Ken made a set from 80 to 600 grits with Velcro and cushion foam from Klingspor. The foam has Velcro on both sides to adhere to the wood above and attach to the removable Abranet disks below.
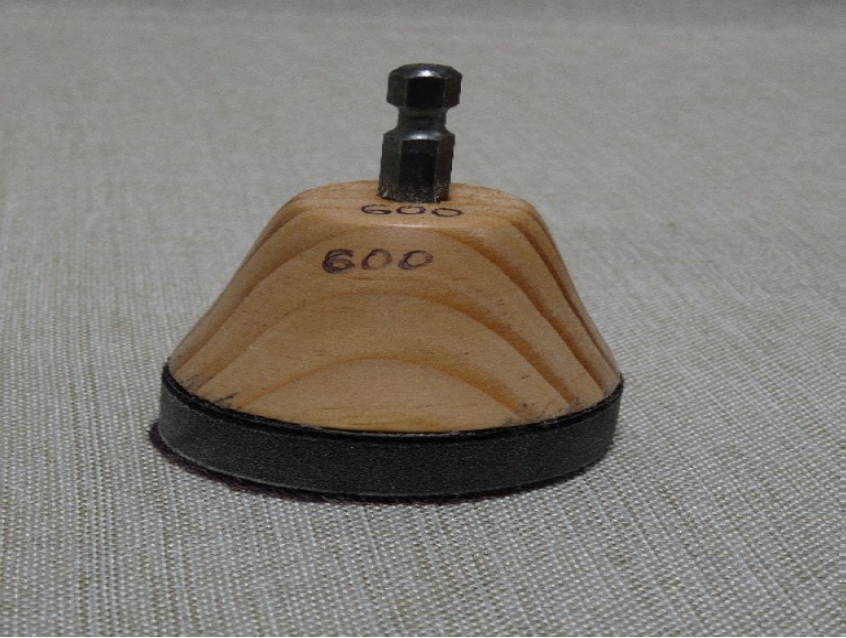
The attachment is a DeWalt quick connect drill bit (not anodized) from Home Depot that has been epoxied into a predrilled hole. He secured the bit in the lathe and then turned the scrap of wood so it was balanced.
The only problem he’s had was the 80-grit overheating and melting part of the foam. Someone mentioned a YouTube video on using a skew to true off the foam so he could possibly reuse it.
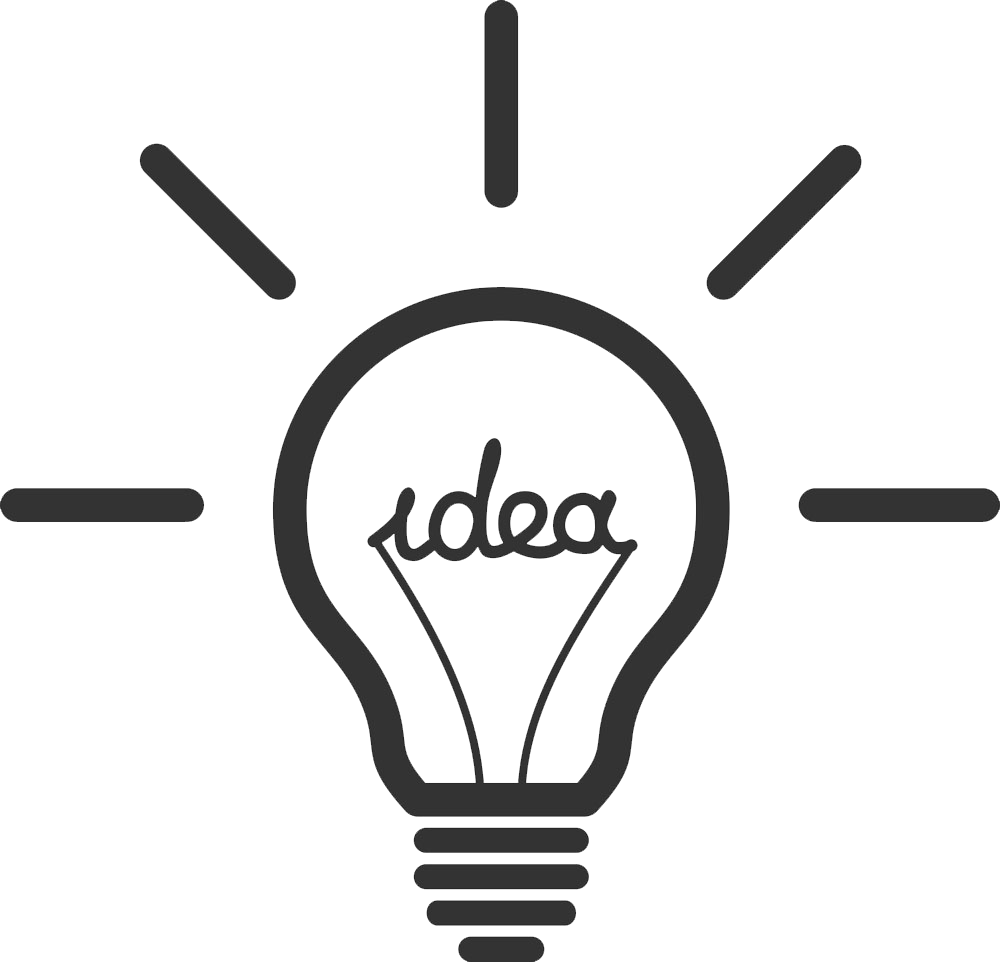
More ideas to be shared at the October meeting!