Today’s topic concerned the different ways members finish their projects. Finish recipes vary from simple to complicated recipes and may be applied using different techniques.
Bill Lieske
Paul Vietti’s Friction Turning Finish: 1 part white varnish, 1 part linseed oil, 1 part denatured alcoholPaul was a former member of PAW who shared his recipe with Bill and other members when they used to meet in Ed Jones’ shop. Bill has used this successfully with the regular yellowish varnish since he’s never used the white varnish. He did say that white varnish can be found on Amazon or through Home Depot or Lowes, but it’s more expensive. It is a friction finish and is applied while the project is spinning on the lathe. Other members said that Shine Juice is a similar recipe except that it uses shellac instead of varnish. Mylands uses wax instead of linseed oil. The food safe quality of finishes was discussed. AAW articles have stated that finishes manufactured in the US since the 1970s are food safe once they are cured. One way to check is to do the ‘sniff test’; if you can’t smell the finish, it’s cured. The ‘Sniff Test’ to tell if a finish is cured and therefore food safe is discussed in the following AAW article: “Food-Safe Finishes”, by Bob Flexner, American Woodturner Journal, Spring 2008, pages 36-39. The reference on the AAW website is: AW2301p36-39.pdf. The article is also included in the AAW book Getting Started in Woodturning, AAW, 2014, page 151. Some members said to allow about two weeks for finishes to cure. Temperature affects the curing time, making it much slower in the winter time here and faster year-round in Phoenix. M&Ms in a wooden bowl just don’t taste the same if the bowl finish hasn’t cured yet. Interesting facts were given about the food safe quality of shellac which is a natural organic material from insects. This quote from the internet gave more details: “The hard, shiny shells on candies are often made from shellac, a resin secreted by the lac bug. You may know shellac from its more famous work in varnishes and sealants, but it’s also a mainstay in pill coatings, candy, coffee beans, and even the waxy sheen on apples and other fruits and vegetables.” Members said that carnauba wax is also used as candy coatings.Dick Kelly

Ken Allen
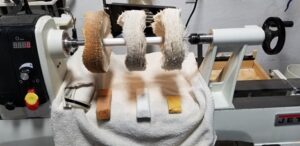
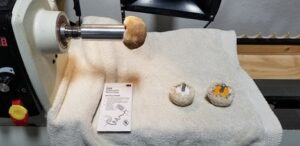
Ken has used the Beall Buffing System successfully for several years and likes the final results of buffing his objects. He’s used it on projects finished with polyurethane, Danish oil and lacquer.
The 3 cloth buffing wheels (first picture) are used on the outside of bowls and other objects. The buffing balls (second picture) are used on the inside of bowls. Both use Tripoli polishing compound (the red material) for the first stage, White Diamond polishing compound (the white material) for the second stage, and Carnauba wax for the final stage. Both the wheel shaft and the buffing ball holder have a Morris taper on the left end for attaching in the headstock spindle. The wheel shaft is also supported by the tailstock. The adaptor, shown in the second photo, fits on the Morris taper. An extension could be added for taller objects like vases.
A thick folded towel is placed on the lathe bed to cushion any damage if an item slips out of my hands when buffing (it has happened!).
The buffing wheels are turned at 1800 rpm and generate static electricity while buffing. To avoid unpleasant shocks, which can be a surprise that causes you to jerk and possibly drop the object, Ken connects a static charge wrist strap between the lathe and his body to bleed off the charge. The strap is shown on the left in the first photo and the package is shown in the other photo. He uses painter’s tape to attach the copper end of the strap to bare metal on the lathe, such as on the lathe bed to the left and below the motor. To prevent the strap from possibly getting wrapped into the rotating parts, he tapes the other end of the strap to bare skin on his left leg near his ankle. This allows some movement while buffing without breaking the connection. This bleeds off all of the static charge and prevents the static shocks. Caution: do not tape the strap to your wrist for use at the lathe because it could get wrapped up on the rotating parts and cause an injury.
This system is quick and easy to set up and use and gives good results. Be sure to let the finish cure sufficiently before buffing. Also, use a light touch to avoid overheating the finish, which can cause some finishes to run, and avoid overly polishing through the finish to bare wood.
The older buffing balls are color coordinated, but new replacements will need to be labeled with markers since they all have white backing.
One member suggested storing them in 8X10 aluminum tins from a thrift shop with one for each polishing compound to keep from cross contaminating the substances.
Jerry Walters
Jerry enjoys making projects out of figured wood and has developed an extensive list of sanding and finishing tips. He shared a few of his beautiful, finished projects. Many of his tips will be listed and discussed after these photos.
Taurus shaped tiger maple finished with Danish oil
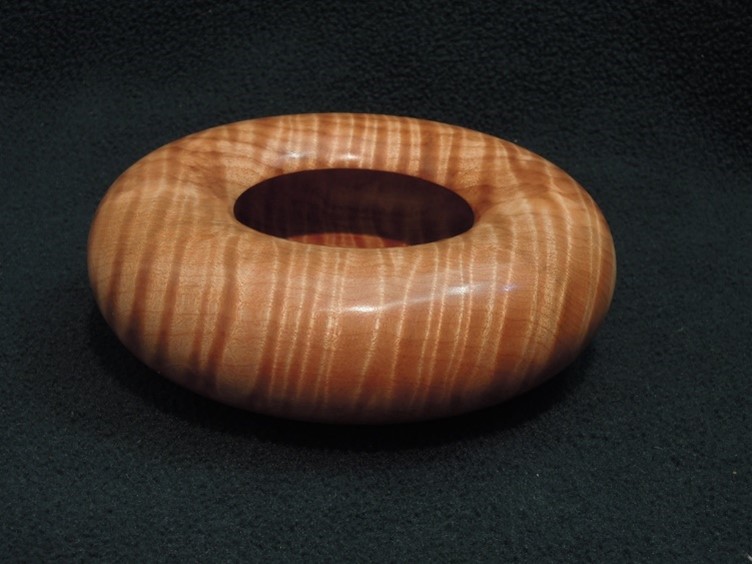
The Beall buffing system was used on this project.

Platter made from a maple burl with copper fill near a bark inclusion
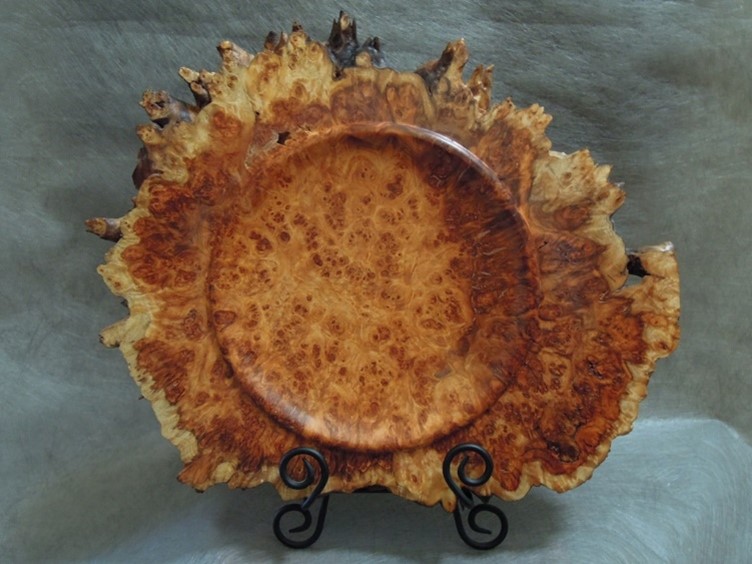
Large cottonwood burl, about 18 inches across

Red burl
Sanding and Finishing Tips: Turning Tips (for a smoother starting finish)
Jaw size – the larger the better: Larger jaws to fit the project will have less vibration in the wood. Many people use the 50 mm jaws for projects where a larger set of jaws would be more beneficial. Shear scraping with swept back gouge: Use fine angel hair cuts. Shear scraping with standard and negative rake scrapers: Choose the correct tool for cleaner cuts. Dealing with tear-out (water / sanding sealer / oil): First sprinkle with water to raise the grain, then coat with sanding sealer, use walnut oil then, finally, sheer cut the surface. With large platters (or thin walls), work in a few inches at a time: Leave it thick, then clean cut a section at a time.Sanding & Finishing
Embrace the process! Lung protection!! Fine sanding dust can damage the lungs. Use a dust collection system and dust masks. Sand at a slow speed!! – 200-350 rpm (lathe and power sander) Whether using hand or power sanding, you want to feel the paper catching on the wood as it sands. If you go too fast, it skips across the grains or can heat up the wood. He usually sets his lathe to 100 rpm and the drill at ~200 rpm when power sanding. Sand through all of the grits – do not skip! Spend more time at the rougher grits. Don’t move to a finer grit too soon (clean between grits): Clean between grits with a paint brush or air compressor. There are scratches that you don’t see until you move to a finer grit. Sanding creates a fine powder that goes into the scratches. It doesn’t take much pressure to force the dust into the wood. Do not hesitate to go back a grit (or two!) Use a backing pad! Many use leather, foam, a flipflop… Jerry’s finishing schedule for figured wood Sanding to 180 “Whiskering”: wet with water to bring up the fibers so you can sand off those ‘hairs’ More sanding to 240 Sanding sealer — (clean thoroughly before applying!) More sanding to 320 Sanding sealer — (clean thoroughly before applying!) More dry sanding 320/400 Walnut Oil sanding to 400/600: walnut oil acts as a sanding lubricant that soaks into the grain; fine fibers when sanding can clog the sandpaper or Abranet; clean with a toothbrush Danish Oil – 00/000 Abrasive pad as applicator: has linseed oil in it; Danish oil pops out the figures in wood. Polyurethane is a water-resistant finish that can be used after the oil has cured and gives it the shine. Drying time Buffing/polishing: If using Tripoli and it’s gummy, it’s too early to buff because the surface hasn’t cured. Oil based varnishes may be applied over Danish Oil. Other tips: Jerry’s formula for finish: 2 parts walnut oil, 1 part Minwax silver polyurethane and 3 parts thinner. To see if there are scratches at the fine grits of 320-400, leave the project on the chuck and take it out to look at it in the sunlight. If there are scratches that show up due to damage during buffing, walnut oil can be used to fill areas and then sand 400-600 grits. The quality of the wood affects the results. Jerry has some informational handouts in pdf format that members can have if they are interested. One has a few charts that identify the best sanding speeds based on the diameter of the project (sanding speed by diameter). Another is a chart that identifies the amount of denatured alcohol to mix with shellac flakes (shellac cuts). He also has an excellent chart that compares the properties of various finishes, their ease of use, drying and curing times, as well as other details (woodturning finish properties). Members can request copies of those handouts from Jerry Walters, Mark Oglesby or Kathy Allen. Meeting notes by Kathy Allen